Este processo tem como objetivo decompor as bifenilas policloradas existentes em óleos contaminados com estes produtos.
O sistema pode processar óleo contaminado com até 2000 mg/kg para valores inferiores a 2 ppm que caracteriza um óleo como não contaminado, o melhor “isento de PCBs”, conforme Norma ABNT NBR 8371, e a Lei 12.288 de 22/02/2006.
O processo de descontaminação baseia-se na reação entre o sódio elementar com as bifenilas policloradas formando bifenilas, cloreto de sódio e hidróxido de sódio.
Este processo tem como 2 objetivos:
- A Destinação final dos óleos “Certificada” sem sua destruição como no processo de incineração, permitido a sua reciclagem, com custos inferiores a incineração, que consome combustíveis não renováveis e contribuição ao efeito estufa;
- A possibilidade de se regenerar os óleos após a sua descontaminação, o que é exigida pela Lei 12.288 de 22/02/2006. Assim os óleos contaminados com PCBs, podem ser reutilizados após a sua descontaminação e posterior regeneração.
O óleo contaminado ao ser recebido nas instalações da TECORI será armazenado num reservatório de 20 mil litros.
O processo se inicia por uma filtragem, onde serão retirados sólidos e a água livre seguindo para um secador que promoverá a secagem da água dissolvida. O óleo retorna ao tanque em circuito fechado até a eliminação total da água.
Uma vez desidratado, o óleo é enviado pela bomba dosadora para a sessão de reação passando primeiramente pelos aquecedores elétricos para o aquecimento de ativação da reação. O óleo fica recirculando pelos aquecedores até atingir a temperatura de 130 oC. Antes de entrar no reator centrífugo, a corrente recebe a adição dosada de reagente (emulsão de sódio metálico em óleo mineral) através da bomba dosadora, com também a adição de uma solução aquosa de álcool isopropílico através de uma bomba dosadora, o qual tem a função de favorecer a reação.
Na fase de reação, num tempo muito curto ocorre também a reação entre a água e parte do sólido, produzindo H+ que será necessário na substituição do cloro no PCB gerando NaCl, NaOH e bifenila.
Após a reação, o óleo aquecido é resfriado no trocador e posteriormente recebe uma adição de água. A função desta água é eliminar o sódio remanescente, gerando, no entanto H2 e mais NaOH. Uma adição de CO2 na corrente promove o “stripping” do H2 através do vaso separador gás/líquido. O efluente gasoso, contendo apenas CO2, H2 e H2O é dirigido para descarte em sistema de adsorção com carvão ativo. As fases líquidas, água / óleo são separadas nos vasos separadores.
O óleo descontaminado é enviado ao vaso de espera, onde é analisado, e em se confirmado o teor de PCBs inferior a 2 mg/kg (isento de PCBs), o mesmo é enviado para venda, reciclagem e ou regenerado para reúso como óleo dielétrico.
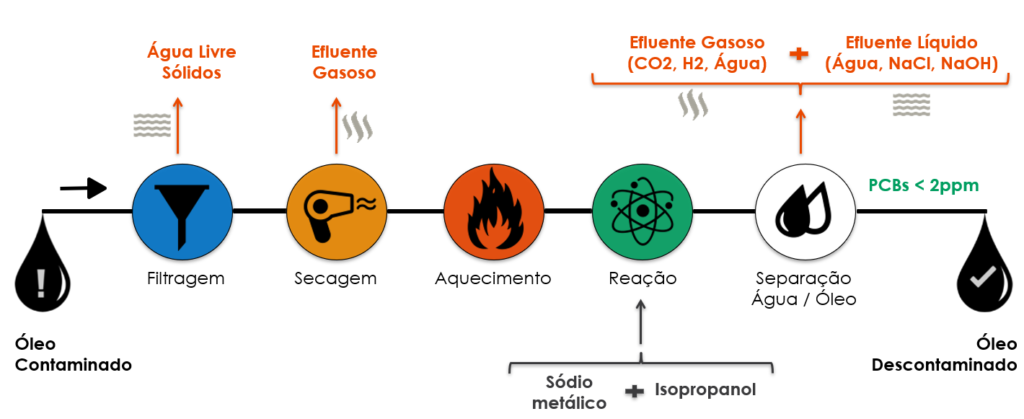